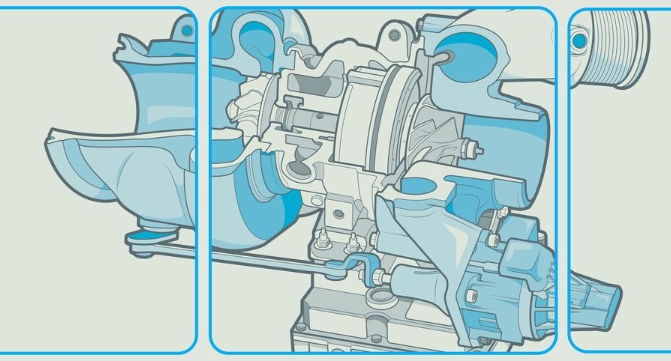
Revolutionizing Internal Combustion: The Impact of Electric Turbochargers
In the pursuit of efficiency, automotive engineers are constantly seeking innovative solutions. One such solution is the electric turbocharger, which has the potential to revolutionize internal-combustion engines. While traditional turbochargers have been widely used to increase power and efficiency, they also come with their limitations. Electric turbochargers offer a new approach to overcome these limitations and unlock even greater performance gains. Let’s explore how electric turbochargers are changing the landscape of internal combustion engines.
Traditional turbochargers have their drawbacks. They can be slow to spool up, their performance is solely dependent on exhaust gas flow, they waste exhaust gases, and they generate heat. Additionally, they can only operate within a certain speed range to avoid potential damage to the turbocharger and engine. These limitations highlight the need for innovation in turbocharger technology to overcome these challenges and unlock greater performance potential.
An electric turbocharger can offer solutions to these challenges and more. Let’s take a quick recap of turbocharger basics. A traditional turbocharger consists of two turbines within a snail-shaped housing, connected by a small shaft. Exhaust gases flow over one turbine, known as the exhaust turbine, which in turn drives the other turbine called the compressor wheel. The compressor wheel increases the air density in the intake, boosting engine power. Fresh air is also fed into the compressor, and typically, the compressed air passes through an intercooler to lower the intake air temperature. On the exhaust side, there is usually a wastegate valve that opens to release excess air downstream to the exhaust system once the turbine reaches the desired speed. However, an electric turbocharger operates differently, powered by an electric motor instead of exhaust gases, and offers unique advantages in terms of performance and efficiency.
An electric turbocharger is essentially a traditional turbocharger with an electric motor integrated into the turbine shaft. While the concept may seem simple, its execution can be challenging, yet filled with potential.
“It brings another degree of freedom,” says Craig Balis, CTO at Garrett Motion, in an interview with Road & Track. “Automakers can leverage it for power, efficiency, emissions, and drivability.”
This innovation opens up new possibilities for automotive engineers to optimize performance, fuel efficiency, emissions, and overall drivability in their vehicles.
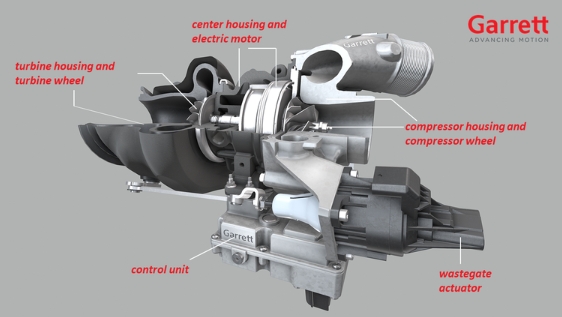
With years of experience in the turbo industry, Garrett was the pioneer in introducing electric turbochargers to the market. Mercedes-AMG took the lead as the first automaker to adopt this technology, offering it in their C43 and C63 models. These vehicles are powered by AMG’s 2.0-liter M139 engine, paired with an e-turbo to generate an impressive output of 402 hp and a staggering 476 hp, respectively. In fact, the C63 boasts the highest power density engine currently available, with 251 hp per liter. As if that wasn’t enough, the four-cylinder engine is further enhanced with a plug-in hybrid system, resulting in a jaw-dropping 671 hp.
It’s a common misconception to think that the sole purpose of an electric turbocharger is to reduce turbo lag. While that is indeed a significant benefit, there’s more to it than meets the eye. In simple terms, a larger turbocharger with bigger turbine and compressor wheels can deliver more air to the engine, resulting in increased power. However, larger turbos also take longer to reach the target boost level, causing lag. But with the addition of an electric motor to the turbocharger shaft, the entire assembly can reach maximum speed without relying solely on exhaust gases. This means that turbo lag, while not entirely eliminated, can be reduced to such a negligible level that it’s inconsequential.
Balis favors the term “transient response” over “turbo lag” when referring to the effects of pressing the accelerator. He highlights that enhancing transient response not only enhances drivability, but also has positive impacts on emissions.
“By precisely controlling the air that enters the engine, we can better match it with the fuel and the engine’s demand, resulting in improved overall performance and reduced emissions.”
Furthermore, an electric turbocharger brings significant efficiency gains. The electric motor can operate in two directions, including spinning in reverse to function as a generator. This feature is commonly utilized in hybrid and battery-electric vehicles, where the energy generated during motor braking is fed back into the battery to recharge it. Similarly, the electric motor of an e-turbo can also be used to recover energy during deceleration.
“The interesting thing about the turbo is that over different drive cycles, it can be energy neutral,” explains Balis. “This means that it can generate as much energy as it consumes. It may vary at different points in time, but over various drive cycles, it can become energy neutral, or even energy positive.”
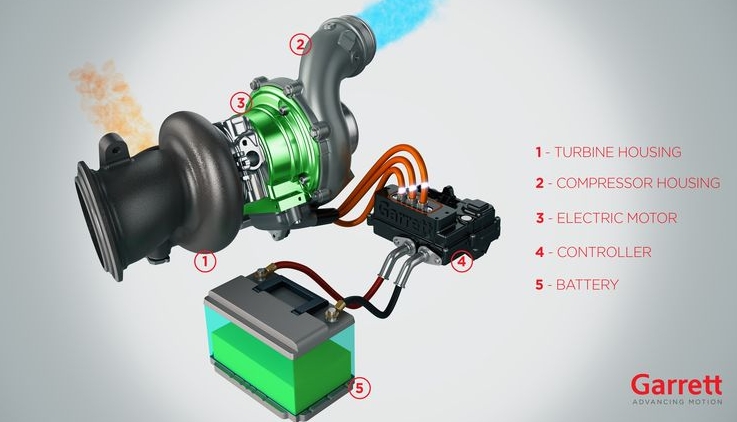
While Garrett’s electric turbocharger still incorporates a wastegate, the precise control of boost pressure minimizes wasteful exhaust gas release, allowing for a smaller wastegate to be used. With an electric motor on the shaft, the turbocharger’s speed can be accurately determined at all times. In conventional setups, a vehicle’s Engine Control Unit (ECU) estimates the turbocharger speed and uses the wastegate to manage boost pressure, but leaves a significant margin for error to ensure safety and durability. This cautious approach often leaves performance potential untapped for a given turbocharger size. However, with the exact speed of the turbocharger known in an electric turbo, it can be operated much closer to its optimal limit without the risk of exceeding it. It’s worth noting that while this benefit is not unique to e-turbos, as Ferrari and Nissan also employ traditional exhaust-gas turbochargers with speed sensors, it is still significant in improving overall performance.
Garrett began researching electric turbochargers two decades ago, but at that time, they were not feasible due to limitations with 12-volt electrical systems. The maximum motor size that could be accommodated on the shaft was only 3 kW, and even then, it placed a significant strain on the system. However, with the advent of higher-capacity electrical architectures, electric turbocharging became a viable option. Many current versions of the C-Class, including the C63 with its AMG-designed plug-in hybrid system, utilize a 48-volt “mild-hybrid” architecture, while the new C-Class exclusively features four-cylinder power. In this context, electric turbocharging proved to be a logical choice, offering improved performance and efficiency without compromising on powertrain choices.
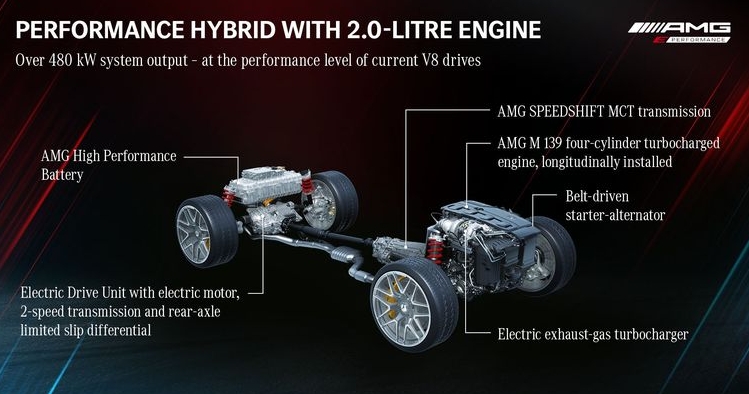
Jan Habermann, one of the engineers responsible for AMG’s implementation of electric turbochargers, revealed that the decision to equip the C43 with an e-turbo was driven by the desire to bestow the car with a unique engine, distinct from its predecessor which shared a V-6 engine with non-AMG models. The M139 engine used in the C43 is handcrafted at AMG’s factory in Affalterbach and is also employed in AMG’s 45-series vehicles. However, unlike those models which use traditional exhaust-gas turbochargers due to their 12-volt electrical systems, the C43 benefits from the advantages offered by the e-turbo technology, such as improved performance, efficiency, and other benefits that the hardware brings, despite producing slightly less horsepower (402 hp compared to the CLA45 S’s 415 hp).
The story of the C63 is distinct. In replacing the beloved 4.0-liter V-8 with a four-cylinder plug-in powertrain, AMG was aware that it needed to deliver exceptional performance. Jan Habermann explains:
“Going hybrid has a lot of advantages. You can have a very small and fuel-efficient engine on one side; you can drive fully electric, and you have really insane performance, much, much, much better than the predecessor.”
AMG recognized that the C63 had to not only compete with traditional gas-powered super-sedans but also with the emerging wave of ultra-powerful EVs. With models like the Kia EV6 boasting 577 horsepower, the decision to go hybrid made strategic sense in this evolving automotive landscape.
Obtaining the desired level of power from a 2.0-liter turbocharged four-cylinder engine, as AMG aimed to achieve with the C63, would result in significant turbo lag with a traditional turbocharger, according to Habermann. The C63’s turbocharger boasts a massive compressor wheel diameter of 71 mm, generating a maximum boost of 37.7 psi, a level more commonly associated with heavy-duty trucks or high-performance tuner cars. It’s an enormous turbocharger, complete with variable-geometry vanes for added flexibility. One might assume that the C63’s hybrid system, featuring a 204-hp electric motor, could compensate for any turbo lag, rendering the use of an electric turbo unnecessary. However, the answer is not that simple.
“As Habermann explains, it’s all about optimizing performance and efficiency.”
AMG’s hybrid system incorporates a 6.1-kWh battery, and the control strategy is designed to maintain sufficient charge in the battery so that the electric motor can deliver full power whenever the driver demands it. By utilizing the electric turbocharger to quickly bring the engine up to full power, the electric motor can then remain on standby with energy stored in the battery.
“It’s an interesting concept,” says Habermann. “You have an electric traction drive, but you don’t actually want to use it in order to store the energy. You only want to use it for performance purposes.”
While it may seem counterintuitive, the logic becomes clear when you take into account that the motor on the C63’s electric turbo is just 6 kW (8 hp) in power. This means that significantly less energy is required to spin it up compared to a drive motor that is 25 times more powerful. This allows for efficient utilization of the electric motor’s power to quickly bring the engine to full power, while preserving energy in the battery for performance purposes, as explained by Habermann.
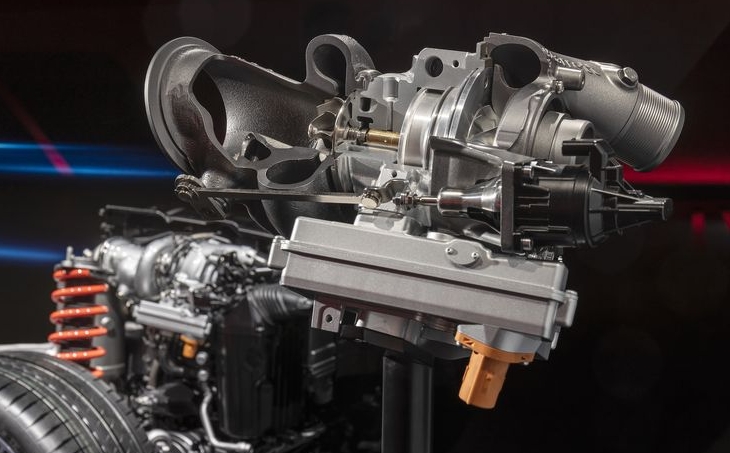
AMG employs a range of intriguing techniques with the turbocharger to optimize performance throughout the engine’s rev range. At low engine speeds, the electric motor spins up the turbocharger while exhaust gas pressure is still building, resulting in increased air volume entering the engine and aiding in boost generation. During constant throttle at around 3500 rpm, the motor’s contribution may be minimal, as there is enough exhaust gas to maintain the turbocharger at its maximum speed of 175,000 rpm. However, as engine speeds climb towards the C63’s 7000-rpm redline, the motor ramps up its output to around 1 kW, keeping the turbo spinning and extending the power band for improved throttle response. This approach allows the C63’s turbo engine to deliver power in a manner that emulates a naturally-aspirated engine, with power building progressively across the rev range, in contrast to the typical drop-off in performance closer to redline observed in many turbocharged engines.
As expected, AMG leverages the electric motor in the turbo to enhance transient response throughout the power band, as needed. According to Habermann, at lower engine speeds, it could take up to a second to reach full boost pressure, while in the mid-range, it’s nearly instantaneous, and at high RPM, it’s reduced to around 0.4 seconds. This is a remarkable feat considering the size of the turbocharger, and Habermann notes that the response is imperceptible to the driver. Furthermore, the turbocharger also regenerates energy back to the battery during off-throttle situations, such as during gear shifts, by capturing the air that would typically be vented out through a wastegate and redirecting it to the battery, thus improving overall efficiency.
Indeed, it’s worth considering the immense challenge faced by the calibration engineers and AMG’s team in ensuring the durability and reliability of a 2.0-liter four-cylinder engine under the extreme conditions of 37.7 psi of boost. Additionally, the engineers responsible for designing the electric motor within the turbocharger face the daunting task of achieving rapid spin-up to 200,000 rpm in an environment characterized by high temperatures and intense vibrations. It’s a testament to their expertise and ingenuity in creating a powertrain that can withstand such demanding performance requirements without compromising on performance or longevity.
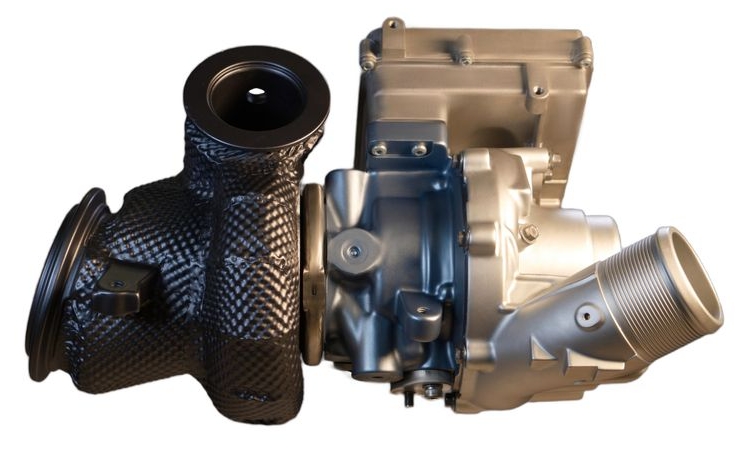
Balis predicts that electric turbocharging will gain wider adoption among automakers in the near future, not just for high-performance vehicles, but also for mild-hybrid and plug-in hybrid cars as they become more prevalent and necessary for meeting emissions regulations. Even truck manufacturers are showing interest in this technology. Balis explains that electric turbocharging offers benefits such as improved efficiency, reduced emissions, higher power density, and greater flexibility in engine design. It provides precise control over air supply, allowing for more precise performance. Moreover, the costs associated with the necessary hardware are decreasing, making electric turbocharging a more viable solution for mainstream applications. This emerging technology is poised to revolutionize engine design and enable new possibilities in the automotive industry.
The future of e-turbos will likely be shaped by the progress of our transition to fully electric vehicles. While they may be seen as an interim solution, e-turbos are also making internal-combustion engines more viable by improving their efficiency. This serves as evidence that there is still untapped potential in internal-combustion engines, and advancements like e-turbos are pushing the boundaries of what is possible. As the automotive industry continues to evolve, e-turbos could play a significant role in optimizing the performance and efficiency of internal-combustion engines, while we continue to work towards a fully electric future.